High-Performance Liquid Chromatography (HPLC) solvent filters play a critical role in ensuring the accuracy and reliability of your chromatographic results. These filters are designed to remove particulate matter and contaminants from solvents, preventing clogging of columns, damage to pumps, and interference with detectors. By maintaining a clean and consistent flow of solvents, HPLC solvent filters help extend the life of your system and ensure optimal performance.
When selecting the right solvent filter for your HPLC system, three key factors must be considered: pore size, connector type, and connector tube size. Each of these factors influences the efficiency, compatibility, and overall effectiveness of the filtration process. In this guide, we’ll explore how to make the best choice based on your specific HPLC requirements.
1. Understanding HPLC Filter: Pore Size in Solvent Filters
What is Pore Size?
Pore size refers to the diameter of the tiny holes or spaces in a filter through which particles can pass. It is typically measured in micrometers (µm). In HPLC solvent filters, the pore size of the filter membrane determines the size of particles that the filter can remove from the solvent before it enters the system.
Definition and Significance in Filtration
In HPLC, maintaining solvent purity is crucial to ensure accurate results and protect sensitive components like columns, pumps, and detectors. Pore size plays a significant role in removing particulate contaminants that could clog the system or interfere with separation efficiency.
0.2 µm vs. 0.45 µm: Differences and Applications
0.2 µm Filters: These finer filters are designed to remove smaller particles and even some bacteria. They provide higher purity and are ideal for ultra-sensitive applications.
Applications:
UHPLC systems: Due to their smaller column particle sizes and higher pressures, UHPLC systems require exceptionally clean solvents to prevent clogging.
Sensitive detectors: Detectors like mass spectrometers (MS) or UV detectors with high sensitivity benefit from cleaner solvents to avoid baseline noise or artifacts.
0.45 µm Filters: These are slightly less fine and are more commonly used in general HPLC applications where ultra-fine filtration isn’t necessary.
2. Choosing the Right Connector Type for HPLC Systems
Types of Connectors:
When setting up an HPLC system, choosing the right connector ensures proper solvent flow, minimizes leaks, and maintains system integrity. Here are the common connector types:
Luer-Lock ConnectorsThese connectors feature a twist-lock mechanism, offering a secure and leak-free connection.
Slip-Tip ConnectorsAlso known as push-fit connectors, they rely on friction to hold components together, without any locking mechanism.
Barbed ConnectorsDesigned with ridges or “barbs” that grip onto flexible tubing when pushed in, ensuring a tight seal.
In addition to connectors, inlet solvent filters play a crucial role in preventing pump cavitation and protecting the system from particulate matter.
Advantages and Disadvantages of Each Connector Type
Here’s a table based on your content:
Connector Type | Advantages | Disadvantages |
---|---|---|
Luer-Lock | – Secure, leak-proof connection. – Easy to assemble and disassemble. – Standardized for compatibility. – Helps optimize processes and filtration costs. | – May require adapters for some HPLC systems. – Can wear out over time with frequent use. |
Slip-Tip | – Quick to connect/disconnect. – Simple design, no additional components. | – Less secure, prone to leaks under high pressure. – Not suitable for high-pressure HPLC systems. |
Barbed | – Strong grip on flexible tubing. – Good for low to moderate pressure applications. | – Difficult to disconnect once attached. – Tubing can be damaged during removal. |
Matching Connectors to Your HPLC System
Ensuring Proper Fit and Leak-Free Connections
Check Manufacturer Specifications: Always refer to the HPLC system or column manufacturer’s guidelines for compatible connectors.
Tubing Compatibility: Ensure the connector matches the tubing material (e.g., PTFE, PEEK, stainless steel) and size.
Test for Leaks: After installation, run a solvent through the system at low pressure to check for leaks before starting full operations.
Solvent Inlet Filters: Use solvent inlet filters to protect the system by filtering solvents, preventing pump cavitation, and avoiding damage to expensive hardware.
Conclusion
Selecting the right connector type for your HPLC system is essential for maintaining system performance and ensuring accurate results. Luer-lock connectors offer secure connections ideal for most HPLC setups, while barbed connectors are better suited for flexible tubing in lower-pressure environments. Always consider the pressure requirements and solvent compatibility when choosing connectors to prevent leaks and maintain system integrity.
3. Selecting the Correct Connector Tube Size for HPLC Systems
Importance of Tube Size in Solvent FiltrationTube size plays a crucial role in HPLC solvent filtration, directly affecting flow rate, system pressure, and overall system performance. Choosing the correct size ensures smooth solvent delivery, prevents leaks, and maintains consistent chromatographic results. Additionally, regenerated cellulose filter membranes are essential for solvent filtration in HPLC applications due to their hydrophilic properties and compatibility with removing particulates from liquid media, which is particularly important in maintaining the integrity of solutions in Biopharma settings.
Impact on Flow Rate: Larger inner diameters (ID) allow higher flow rates, reducing resistance, while smaller IDs limit flow but provide better control and precision in high-sensitivity applications.
Impact on System Pressure: Smaller tube sizes can increase backpressure, especially in high-flow or viscous solvent applications. Conversely, oversized tubing may reduce pressure but can introduce dead volume, affecting peak shapes.
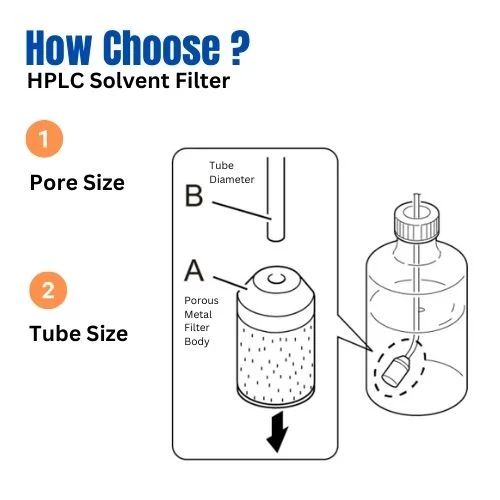
Common Tube Sizes and Their Applications
1/16″ Tubing (ID ~0.005″ to 0.02″)
Applications:
Standard in most HPLC systems.
Ideal for analytical HPLC, where precise control of flow rates is critical.
Used for high-pressure connections in UHPLC systems.
Benefits:
Minimizes dead volume.
Provides optimal peak resolution.
1/8″ Tubing (ID ~0.03″ to 0.062″)
Applications:
Used in preparative HPLC where higher flow rates and larger sample volumes are common.
Suitable for low-pressure solvent delivery systems or waste lines.
Benefits:
Supports higher flow rates.
Reduces system backpressure in high-volume applications.
Other Sizes (e.g., 1/32″, 3/16″)
1/32″ Tubing: Used in micro and nano-HPLC applications, providing extremely low flow rates for high-sensitivity analysis (e.g., proteomics, metabolomics).
3/16″ Tubing: Generally for bulk solvent transfer or waste management in large-scale systems.
4.Matching Tube Size to Your HPLC System
Ensuring Compatibility with Pump and Tubing Dimensions
Pump and Detector Requirements: Verify the tubing size recommendations from your HPLC system manufacturer to ensure optimal performance and avoid leaks.
Connector Compatibility: Ensure that connectors and fittings (e.g., nuts, ferrules) are designed for the selected tubing size, as mismatched components can cause leaks or pressure inconsistencies.
Column Connection: Analytical columns typically require 1/16″ tubing for precise solvent delivery, while preparative columns may use larger tubing.
Conclusion
Choosing the correct connector tube size is essential for maintaining optimal flow rates, system pressure, and chromatographic performance. While 1/16″ tubing is standard for analytical HPLC, larger sizes like 1/8″ are better suited for preparative systems or bulk solvent transfer. Always ensure compatibility with your HPLC components and avoid tubing that could cause backpressure or introduce unnecessary dead volume, safeguarding both system efficiency and data accuracy.
5. Practical Tips for Choosing HPLC Solvent Filters
Selecting the right solvent filter for your HPLC system is crucial for maintaining system integrity, protecting components, and ensuring reliable results. Here are some practical tips to guide your selection process:
Consider the pore size of the filter to ensure it can effectively remove particulate matter without affecting the flow rate.
Evaluate the chemical compatibility of the filter material with the solvents you are using to prevent degradation or contamination.
Assess the pressure rating of the filter to ensure it can withstand the operating pressures of your HPLC system.
Filtering: Emphasize the importance of filtering in the organic solvent filtration process within the fine chemical industry. Filtration is crucial at various stages of synthesis, addressing the complexities involved in designing filtration systems for hazardous solvents. Consider factors like temperature and chemical compatibility when choosing suitable filter cartridges.
Assessing Your HPLC System Requirements
Flow Rate Compatibility
High Flow Rates: For preparative HPLC or systems requiring large solvent volumes, choose filters with larger surface areas or lower pore resistance to maintain efficient flow.
Low Flow Rates: Analytical or micro-HPLC systems benefit from finer filters (e.g., 0.2 µm) to ensure maximum purity without compromising flow.
Pressure Tolerance
High-Pressure Systems (e.g., UHPLC): Use filters specifically rated for high pressures to prevent ruptures or leaks. PTFE or stainless-steel filters are often preferred for their durability.
Standard Pressure Systems: Most general-purpose filters suffice for conventional HPLC, but always check the pressure rating.
Solvent Compatibility
Organic Solvents: PTFE filters are chemically resistant and ideal for aggressive solvents like acetonitrile or methanol.
Aqueous Solutions: Nylon or PVDF filters are better suited for water-based solvents, though compatibility with specific pH ranges should be verified.
Optimize Processes and Filtration Costs
Proper selection and use of solvent filtration cartridges can optimize processes and reduce filtration costs, enhancing overall operational efficiency and performance.
Conclusion
Choosing the right HPLC solvent filter involves balancing system requirements with performance and cost considerations. By assessing flow rate, pressure, and solvent compatibility, consulting manufacturer guidelines, and validating filter performance, you can ensure optimal system operation and reliable analytical results. Investing in high-quality filters might seem costly upfront but will save time, resources, and system components in the long run.